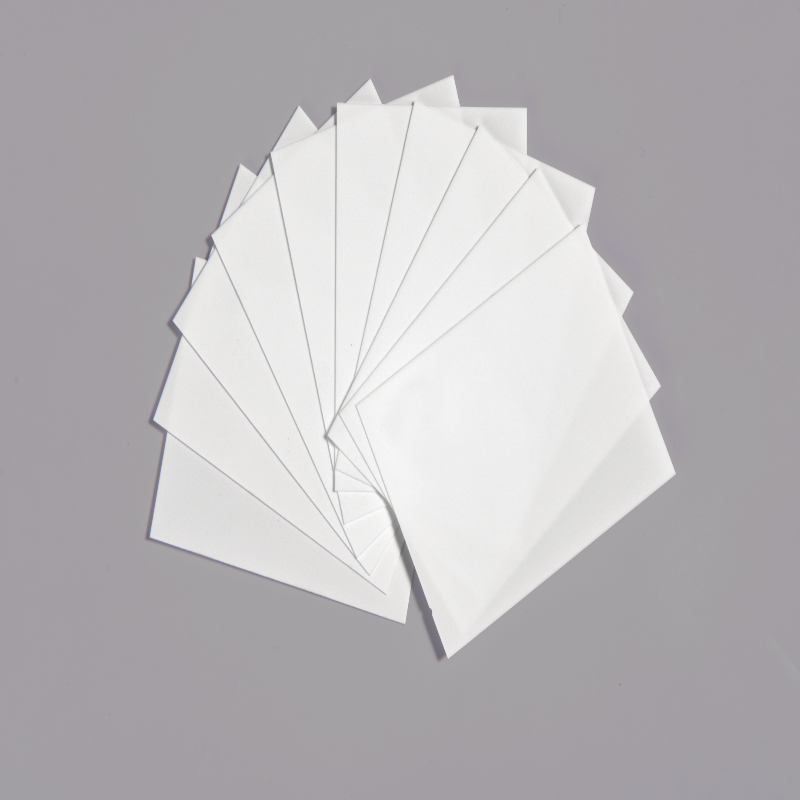
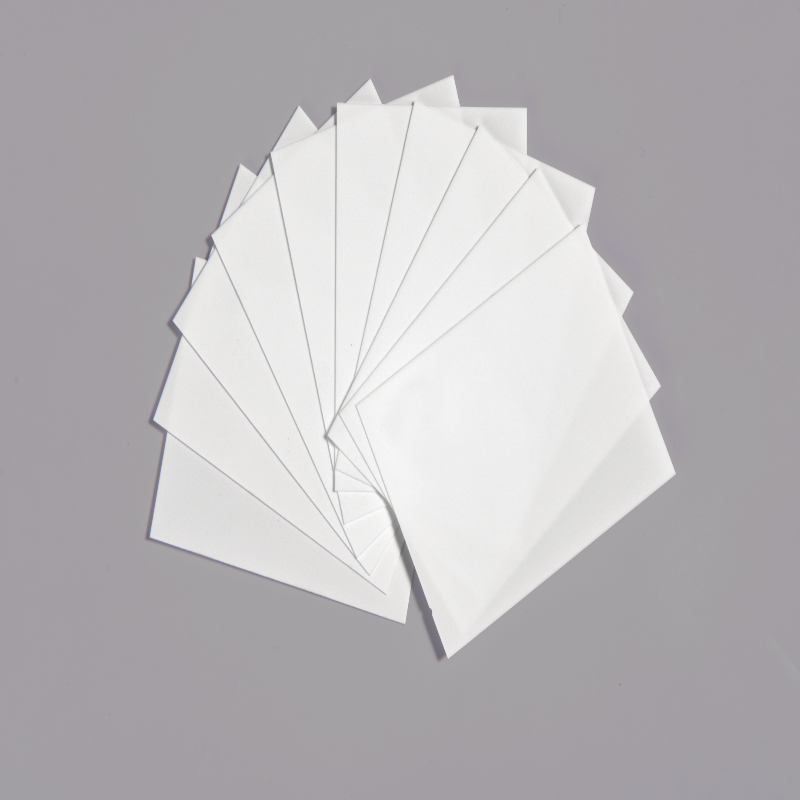
Get Your Custom Alumina Substrate
Aonuo is a trusted manufacturer of Alumina ceramic substrates with years of experience. It specializes in manufacturing high-quality custom Alumina ceramic substrates to cover the various needs of customers. Here are your custom selections:
Features that Our Alumina Substrate Unique
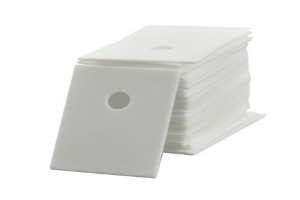
High Thermal Conductivity
- Effective Heat Dissipation: Alumina ceramic substrates have excellent thermal conductivity, which allows them to dissipate heat generated by electronic components efficiently. This is crucial in high-power and high-frequency applications where thermal management is critical.
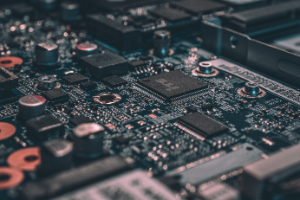
Excellent Electrical Insulation
- High Dielectric Strength: Alumina is an excellent electrical insulator with high dielectric strength, which prevents electrical breakdown and ensures the reliable operation of electronic circuits.
- Low Electrical Loss for High-Frequency Applications: The material’s low dielectric loss makes it an ideal choice for high-frequency applications, such as in telecommunications and radar systems.
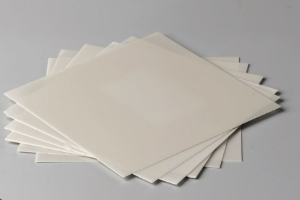
Mechanical Strength and Durability
- High Hardness: Alumina is a tough material, which makes it resistant to wear and mechanical damage.
- Structural Integrity: It has high mechanical strength, allowing it to withstand physical stress and maintain structural integrity under various conditions.
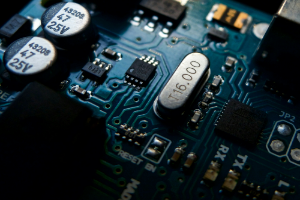
Chemical Stability and Corrosion Resistance
- Inert Material: Alumina is chemically inert and corrosion-resistant, even in harsh environments. This ensures long-term stability and reliability in various applications.
- High Oxidation Resistance: Alumina substrates are ideal for use in oxidative environments due to their high oxidation resistance.
Manufacturing Process of Alumina Substrate
The production process of alumina ceramic substrates involves several key steps:
Powder Processing: Alumina powder is mixed with binders, plasticizers, and solvents to form a homogenous slurry.
Ball Milling: The mixture is ground into a fine powder to achieve the desired particle size distribution.
Tape Casting: The alumina slurry is cast into thin layers on a flat surface, forming green ceramic sheets after drying.
Pressing: The alumina powder is pressed into molds to create green bodies with the desired shape.
Air Drying: Green bodies are exposed to air at room temperature to remove solvents.
Controlled Drying: Performed in controlled environments to prevent cracking and ensure uniform drying.
Pre-Sintering: Green bodies are heated to burn off organic binders.
Main Sintering: Heating to high temperatures (typically 1500°C to 1800°C) to densify and strengthen the material.
Machining: Grinding and polishing to achieve the required thickness and surface finish.
Metallization: Applying metal layers for electrical connections using screen printing or vapor deposition methods.
Inspection and Testing: Checking for defects and electrical and thermal performance testing.
This process results in high-quality alumina ceramic substrates used in electronic applications for their excellent thermal and electrical properties.
GET A FREE QUOTE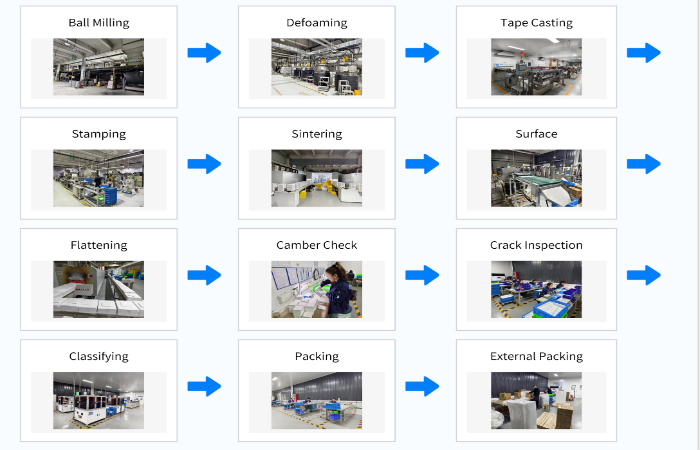
Our Certificates of Alumina Substrate
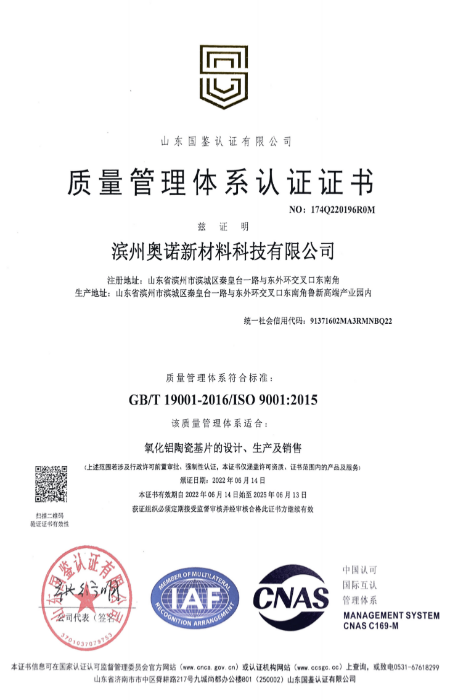
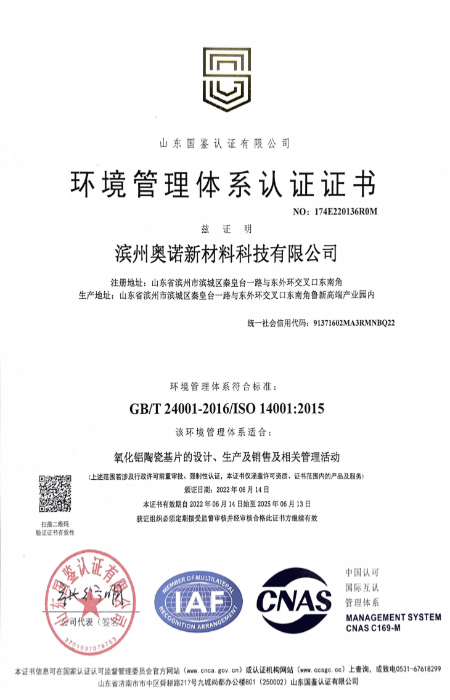
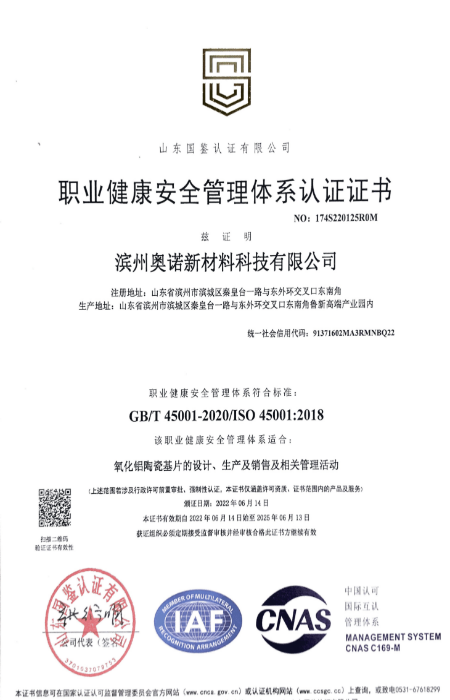
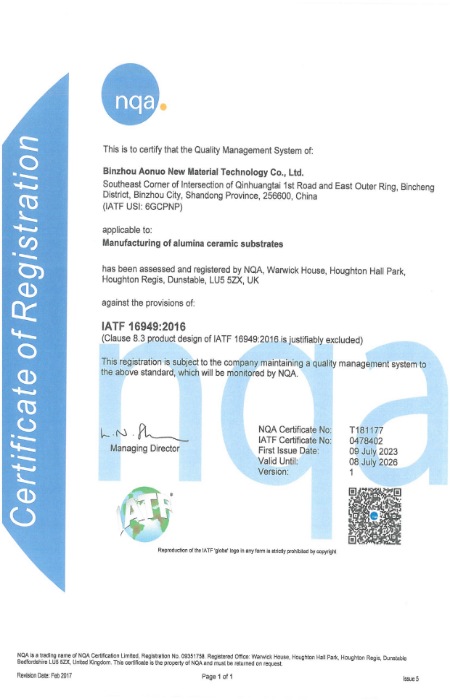
Ready to Get the Perfect Alumina Substrate For Electronic?
Contact Us to Get A Free Consultation
Alumina Substrate FAQs
Alumina substrates have high thermal conductivity, typically ranging from 20 to 30 W/mK, making them suitable for applications requiring efficient heat dissipation.
Alumina substrates are excellent electrical insulators, with a dielectric constant of around 9.8 and a dielectric strength of 15-30 kV/mm.
Alumina substrates are available in various thicknesses, commonly ranging from 0.25 mm to 1.0 mm, depending on the application requirements.
We mainly produce alumina ceramics with a purity of 96%. We can also send you alumina ceramics with a purity of 99% and 99.5%. If you have other needs, you can also ask us.
Flexural Strength
- Flexural Strength: The flexural strength of alumina ceramic substrates generally ranges from 300 to 400 MPa (megapascals). This high strength makes alumina suitable for applications where the material will be subjected to bending or flexural loads.
Hardness
- Hardness: Alumina ceramics are known for their high hardness, which typically ranges between 15 and 19 GPa (gigapascals) on the V